Convert Plastic Waste into Oil with Continuous Pyrolysis
Turn plastic waste into valuable resources with advanced continuous pyrolysis technology, designed for efficiency and sustainability.
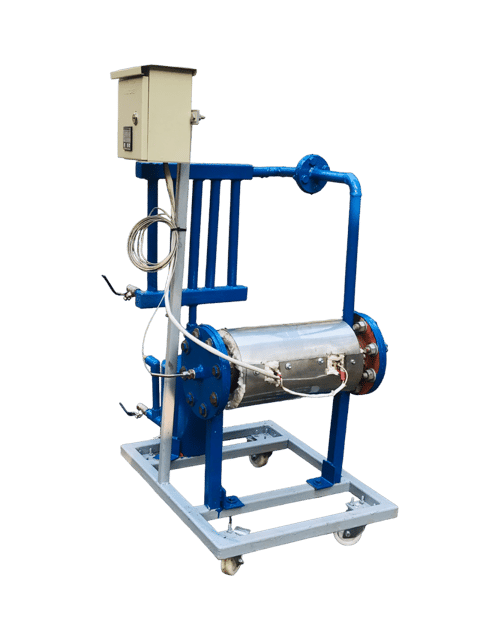
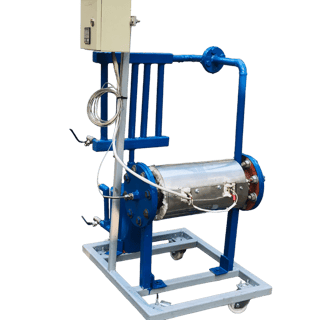
Continuous Plastic Pyrolysis
SCREW MACHINE
VEERA PYRO D
VEERA PYRO LAB
Continuous plastic pyrolysis is an advanced process that continuously converts plastic waste into valuable resources through thermal decomposition. This process takes place in an oxygen-free environment, preventing combustion and harmful emissions. The waste is broken down into its chemical components and transformed into pyrolysis oil, gas, and carbon black, which can be utilized in various industries.
Unlike traditional batch models, where processing must stop to load and unload materials, continuous systems ensure an uninterrupted flow, allowing for constant feeding and extraction. This innovation leads to higher throughput, greater energy efficiency, and reduced operational labor.
The Process of Continuous Plastic Pyrolysis
Feedstock Preparation:
Plastic waste is collected, sorted, and prepared by shredding it into smaller pieces for easier handling and feeding into the system.
Continuous Feeding Mechanism:
The plastic is continuously fed into a reactor chamber where the pyrolysis process occurs. There’s no need for manual loading or downtime, allowing for 24/7 operation.Thermal Decomposition:
Inside the reactor, high temperatures break down the plastic molecules into smaller hydrocarbon chains without the presence of oxygen. This prevents burning and keeps emissions minimal.Separation of Output:
The products of pyrolysis—pyrolysis oil, gases, and carbon black—are separated and stored in their respective containers for further use.Emission Control:
Advanced filtration systems capture any byproducts or emissions, ensuring an environmentally friendly process with near-zero waste.
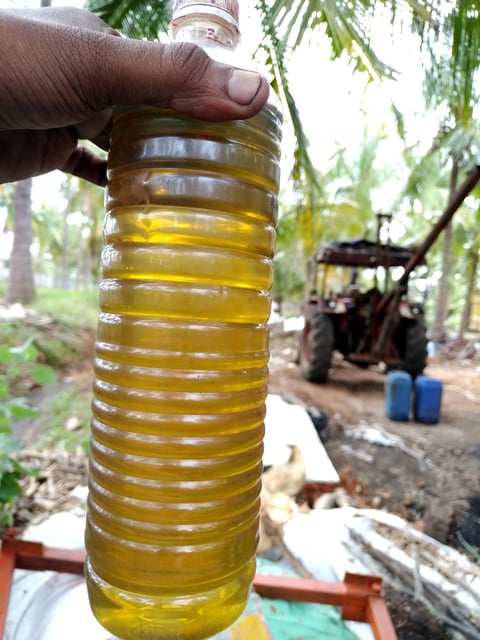
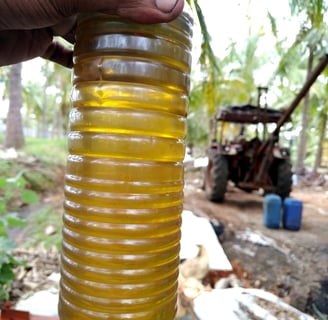
Continuous pyrolysis is a straightforward yet highly efficient process that follows several essential steps to convert plastic waste into usable products:
ABOUT VEERA GROUP
Veera Group is a global leader in sustainable waste-to-energy technologies, committed to transforming how industries approach waste management. With over two decades of expertise, we specialize in providing innovative, eco-friendly solutions that convert waste materials into valuable resources such as fuels and energy. Operating across more than 52 countries, Veera Group's state-of-the-art technologies are designed to meet the unique needs of various industries, offering scalable, cost-effective, and environmentally responsible systems. Our portfolio includes advanced pyrolysis plants, molecular distillation systems, and biomass gasifiers, all of which are engineered with a focus on efficiency, zero waste emissions, and sustainability. With ISO 9001:2015 and CE certifications, Veera Group continues to set new standards in the waste-to-energy sector, driving global change toward a greener, more sustainable future. We are not just transforming waste but also leading the way toward a cleaner planet.
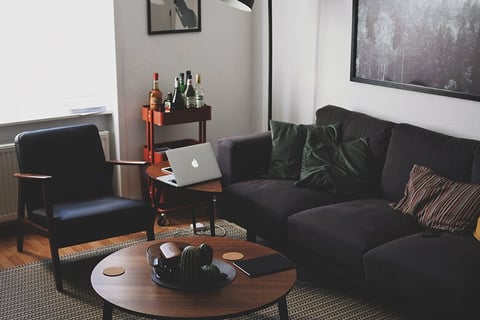
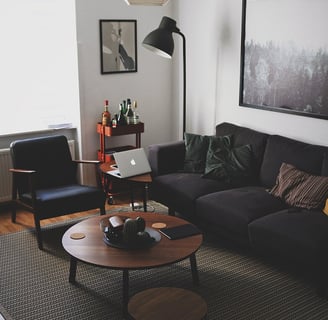
Our Innovative Solutions
At Veera Group, we pride ourselves on delivering cutting-edge technology to meet the world’s evolving waste management needs. Our machines are designed with precision, efficiency, and sustainability in mind, ensuring optimal performance across various industries. Some of our key innovations include:
Plastic Pyrolysis Plants:
These systems convert plastic waste into valuable outputs like pyrolysis oil and gas, helping reduce plastic pollution while generating energy.
Molecular Distillation Units:
A unique technology that efficiently converts waste oils into high-quality diesel, offering up to 85% efficiency and zero waste emissions.
Biomass Gasifiers:
These systems are designed for small to large-scale biomass waste conversion, turning organic materials into clean, usable energy.
Batch and Continuous Systems:
We offer both batch and continuous pyrolysis and distillation systems to suit different operational scales. Our batch systems are ideal for flexible, small-scale operations, while continuous systems provide uninterrupted, high-volume processing for maximum efficiency.
ARE YOU READY FOR CHANGES?
Contact Us
Get in touch to learn about converting our innovative and sustainable products and how they can change your lives.
Phone
+91-9952258626